
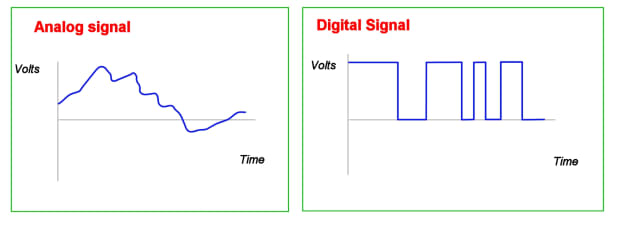
Single-Ended Incremental Rotary Encoder How Do Incremental Optical Encoders Work? This type of encoder utilizes sensors that use optical, mechanical or magnetic index counting for angular measurement. Read more about capacitive encoders in our Capacitive Encoders Guide.Īn incremental rotary encoder is also referred to as a quadrature encoder. Capacitive encoders are available in both incremental and absolute configurations.
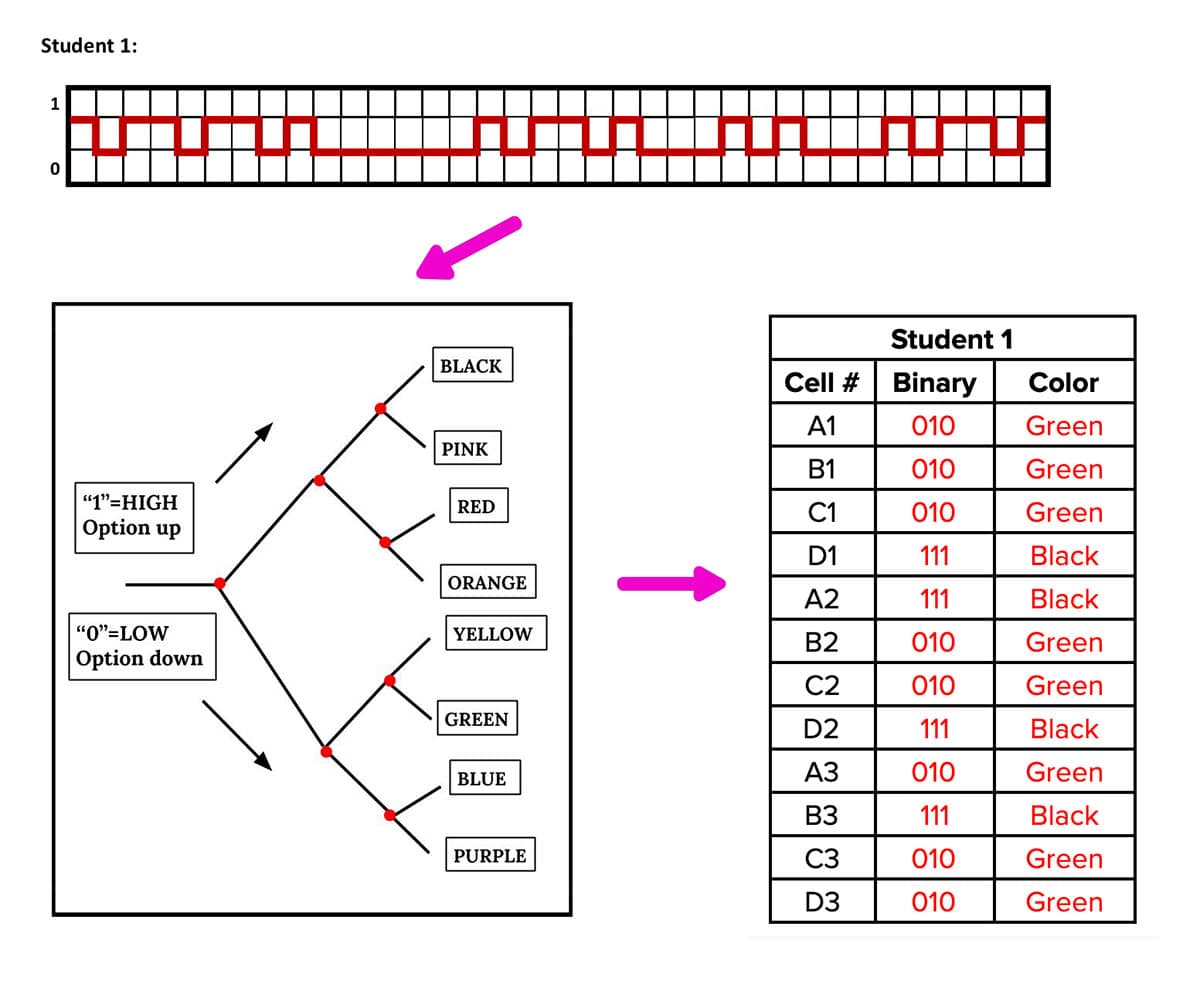
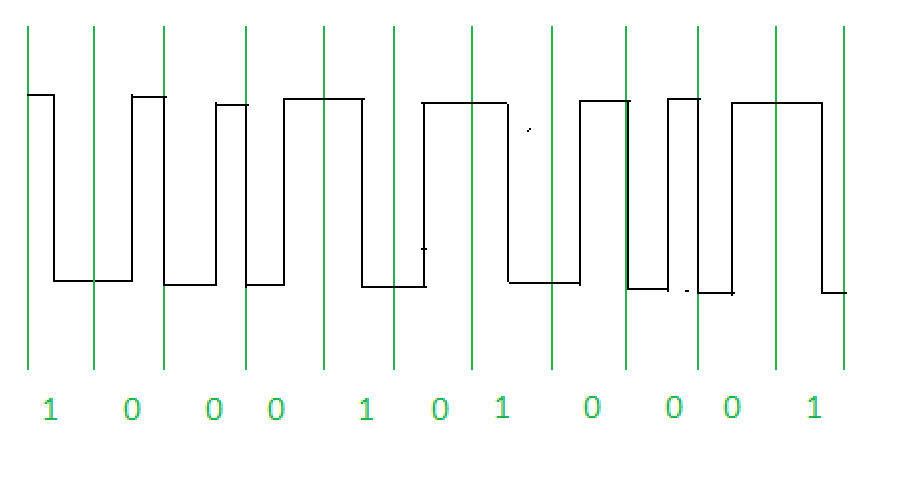
They are less robust and more suited to applications in an environment free of dust and debris.Ĭapacitive encoders combine the best aspects of both optical and magnetic rotary encoders in one rugged, reliable device, but are not suited for large motor shafts (larger than 8mm diameter). They are typically used with linear components, such as blocks and rails. Linear encoders are designed to measure linear motion, rather than rotary motion. Magnetic encoders are available in both rotary and linear configurations. Magnetic encoders are more robust, can operate in conditions with ingress of dirt, dust, oil, and other environmental factors, but do not provide as much resolution as their optical counterparts. Optical encoders are available in absolute, incremental, and commutation configurations. Optical encoders are a cost-effective industry-wide standard that provide precision and accuracy, but may be more susceptible to environmental factors such as heat, shock, dust/dirt ingress. Anaheim Automation offers an array of rotary incremental encoders such as optical, magnetic, and capacitive types, as well as linear magnetic incremental encoders. Ethernet (IP, EtherCAT, ProfiNet, Modbusĭepending on your application requirements, certain types of encoders may be more suitable than others.Fieldbus (Profibus, CANopen, DeviceNet, Interbus, SAE J1939 (automotive).In motion control systems, the most common sensor used is called an encoder.Įncoders provide a measured feedback of mechanical motion (displacement or velocity) to a motion controller. The heating element will have to turn on again to overcome the change in temperature. A disturbance could be as simple as opening the oven door or placing a frozen food item on the oven racks. Disturbances in system processes are measured by a sensor and “fed back” to the PID controller to make the necessary changes to ensure process stability. For example, an oven uses a thermometer to sense when to turn on or turn off a heating element. Encoders are able to provide motion control system users with information concerning position, velocity and/or direction.ĭual-Shaft Motor Without Encoder Dual-Shaft Motor With EncoderĮvery control system leverages some form of sensor feedback. The basic definition of an encoder is a sensor of mechanical motion which generates digital signals in response to motion.
